Friction and Wear Testing
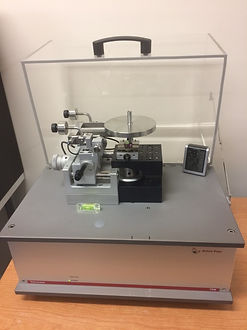


Introduction
Tribology, a Greek origin word, means the interactions between two surfaces in relative motions. In other words, tribology focuses on the study of materials surface friction and wear behaviors as well as how these behaviors alter when lubricants are in action at the interface.

One of the earliest indications of tribology application can be dated back in ancient Egypt 3900 years ago. The carving clearly shows a technician greasing the skids when the pharaoh stature was transported the grave of Tehuti-Hetep, El-Bersheh around 1880 B.C. The tribological studies usually involve solid surfaces, but nowadays the tribo research topics have been extended to many other fields, such as contact lens gels versus eye tissues, human skin against touch screens, etc.. The three major subjects in tribological studies are friction, wear, and lubrication.
Friction, as we experience everywhere and every moment of our lives, is one of the most fundamental yet most difficult studies in the world of physics. Friction by definition is the force against relative movements between two surfaces. There are static friction (like our normal walking) and dynamic friction (like when you slip on a wet floor).
In most cases, friction transits from static mode into dynamic motion. Imagine pushing a heavy box on the ground. At the beginning it is difficult to move, but when the box slides out, it takes less effort to move the box forward). There are so many factors that affect the output of friction, such as temperature, humidity, surface roughness, grease, dust, magnetic force, etc.. Without clearly defining the friction test environments, the friction measurement results could vary drastically.
Wear means the loss of materials due to surface friction. When two solid surfaces wear against each other, based on various interaction mechanisms, the wear can be defined as adhesive wear, abrasive wear, and deformation wear. The wear mechanism gets more complicated when exogenic force or chemical reaction is involved, such as erosive wear and corrosive wear. The instrumented friction/wear lab tests usually focus on the first three "physical" wear studies.
Lubrication is to reduce the friction and/or wear between two surfaces. The study of lubrication is usually combined with friction and wear measurements by adding a third substance (lubricant) at the interface.
Theory
During a pin-on-disc friction/wear study, a sharp pin, ball, or cone tip is employed to wear against the disc surface. Usually a constant normal load is applied from the pin towards the contact interface. The round shape of the tip is to ensure symmetrical contact and reduce any unnecessary stress concentration during friction test. The pin will move back and forth on the disc surface with certain stroke length and speed. A lateral force sensor is usually installed to measure the friction force. The coefficient of friction (µ) is calculated as friction force divided by normal load. The coefficient of friction is a constant and material property. Based on Amonton's law, friction coefficient is independent of normal load applied and the apparent contract area. Also, the Coulomb's Law dictates that µ is also independent of sliding velocity. However the friction coefficient can be influenced by temperature and humidity.

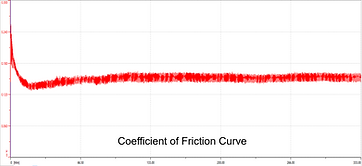
During the friction test, a wear track is gradually made on the sample surface due to the materials loss from friction/wear. The pin/ball tip is usually connected with a high precision depth sensor, so the wear track depth can be measured. Through an optical microscope, the wear track width and length can be accurately measured as well. As the geometry of the wear tip/pin is known, the wear track volume can be estimated. However, a more accurate method is using a stylus or optical profiler to measure the actual volume of loss from the wear track.
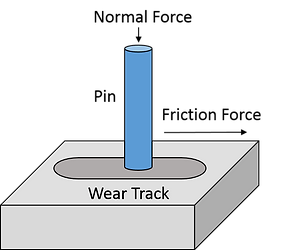

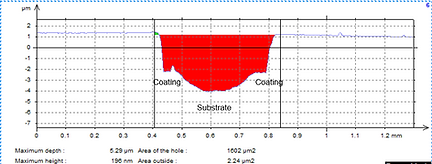
.With the volume of loss (V), travel distance (L), normal load (P), disc material Brinell hardness (H) measured, the wear coefficient (K) can be derived from the equation below. However, the hardness of sample surface is difficult to measure accurately without the influence from sub-layers and substrate, thus the ratio K/H is more practical to represent material wear resistance; K/H ratio is known as the dimensional wear coefficient or the specific wear rate. This is usually quoted in units of (mm3 N−1 m−1). A simplified calculation of wear volume loss is from averaged cross-section area of the wear track (A) and the wear track stroke length (S).

Specific Wear Rate (K/H)=3V/PL
Wear Volume Loss (V)=A*S
High Temp Friction/Wear
In addition to hardness, Young’s modulus and creep behavior, tribological properties (friction and wear) may alter significantly at elevated temperature. The ability to directly assess this behavior at relevant temperatures is an important tool in determining a materials’ suitability for its final application.
The figure below shows how sample tribological behavior changes as temperature increases when the hot stage was used in conjunction with the friction/wear function in testing the sliding wear of a PVD AlTiN coating at high load. The coating fails totally during the third scan at 25 ºC but shows greater ductility at 500 ⁰C and the final wear depth is lower. If you are interested in knowing more about our high temperature friction and wear studies, please contact us!

Advantages
Instrumented friction/wear testing is ideal for small coupons or coating specimens surface tribological study, where conventional high load ball-on-disc tests might be an overkill for ultra thin film structures. The high precision depth and load sensors employed by the friction/wear instruments will accuately dtermine the critical moment of coating wear as well as capture the small and gradual change of friction evolution through sliding test. Also, instead of having a static loading by weight, the instrumented friction/wear function features the automatic control of load applied, which enables some advanced friction/wear (such as step wear) test methods.
Measurements
1. Friction (Lateral) Force
2. Coefficient of Friction (Static and Dynamic)
3. Wear track depth
4. Wear track width
5. Wear track volume (Volume of loss material)
6. Wear rate and wear coefficient
7. Wear resistance
8. Effectiveness of lubricants
Standards
1. ASTM G133 Standard Test Method for Linearly Reciprocating Ball-on-Flat Sliding Wear
2. ASTM G171 Standard Test Method for Scratch Hardness of Materials Using a Diamond Stylus